Structural Analyses of the Wagon Body and Derailment Test
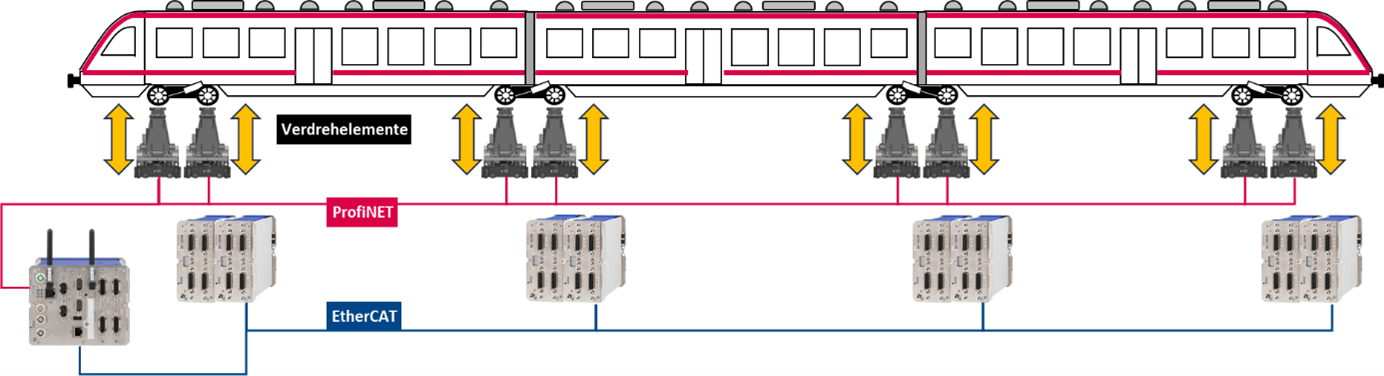
Railroad Test and Validation Center
In cooperation with Brademann + Broistedt GmbH & Co. KG, a torsion test rig for trains was modernized at a validation test center in Germany. This test rig determines the wheel contact forces when the bogies are twisted in order to check for even weight distribution.
Requirements
The project places two key requirements on the modernized test bench: Firstly, it must be able to weigh trains and train elements to determine their weight. Secondly, the wheel contact forces and wheelset contact forces (total forces) must be measured while the train is twisting. In real operations, the train will twist in every curve, as the outer track has a superelevation compared to the inner track. It is particularly important to measure the wheel contact force during these twists, as a wheel contact force that is too low can lead to the train derailing. The imc system combines both requirements in one solution and thus offers an efficient and productive way of meeting the requirements.
- The test stand consists of 8 twisting elements mounted between 2 rails. These elements are each made up of 2 height-adjustable wheel contact surfaces.
- Each side can lift up to 175 kN=17 t, is independent of each other and is controlled via ProfiNET
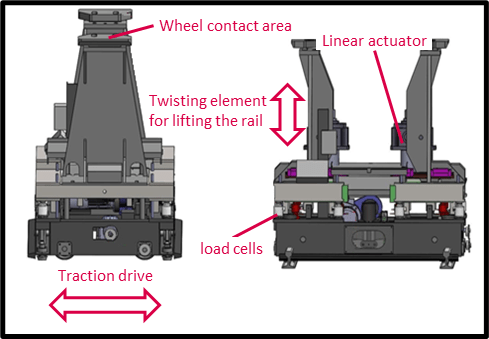
Each twisting element has several drives:
- 2x lifting drive (1x drive per contact surface) to adjust the torsion
- 2x lateral adjustment to move the train in and out
- 1x travel drive to position the elements
- 1x relief drive to lift the torsion element from the rail
The Test Bench
The test bench is considered to be the most modern test center for commissioning, type testing and acceptance of rail vehicles worldwide. In particular, the train must be tested in accordance with DIN 27201-5 on the “Testing of wheel and wheelset contact forces of railroad vehicles” and ORE B55 RP8 “Safety against derailment in track twists”. For the test, the train is driven into the hall of the twisting test stand with 8 twisting elements and parked. A test program loaded in Excel format is then started, in which the train is twisted statically and dynamically in different positions. This is done with the help of 16 (2 per twisting element and 1 per wheel) individually height-adjustable lifting elements, which lift the wheels of the train against each other to different degrees (max. height difference of the wheels 150 mm). The contact force of each individual wheel is measured with the aid of 4 load cells per lifting element during the entire twisting process. By using a leveling device, the position of the wheels can be determined to an accuracy of 1/10 mm. This “starting position” is set manually before the test in order to see the common reference point for all elements in one plane.